Table of Contents Show
What are Biofuels?
Biofuel refers to the liquid fuels produced from biomass (organic matter). Ethanol and biodiesel are two most common forms of biofuel. Biodiesel is made from vegetable oil or animal fat whereas ethanol is derived from corn starch and sugar cane.
Where do biofuels come from?
Biofuels can also be sourced from materials such as wood, agricultural products along with their by-products and waste. Research is still being carried out in search for new sources of biofuel and to improve existing methods of production.
How do Biofuels work?
Biofuels work just like gasoline which can be burned to produce energy which can be used to run cars or heat your homes. The only difference here is that biofuels are sourced from recently harvested plants. This is a major leap in reducing the dependency on fossil fuels.
Further Reading:
Step-by-Step Production Process of Biofuels
There are few basic steps which are followed while making ethanol on a large-scale:
- Fermentation of sugars
- Distillation
- Dehydration
However, the production of biodiesel involves a process called trans-esterification. It involves a chemical reaction of long-chained fatty acids with alcohol which produces fatty-acid esters.
Both of these fuels can be used to fuel cars, trains and aviation.
The biggest problem faced by these biofuels is their lower efficiency and cost-effectiveness as compared to petroleum fuels. Therefore, they are usually used as blends with fossil fuels.
How does biofuel energy work?
Ethanol
To have a better comparison, ethanol is 30% less efficient as per unit of volume than normal fuel. This means that more pure ethanol is required to obtain the same gas mileage as we get from using gasoline. The use of ethanol is restricted to automobiles, trucks and motorcycles for now, specifically for engines which can adapt to ethanol.
Most of the time, ethanol is used as a mixture in gasoline. Mixed fuels are labeled with E- as prefix at the gas stations, followed by the percentage of ethanol mixed in the mixture. For example, E70 means that the mixture contains 70% ethanol and 30% gasoline.
When ethanol is mixed with gasoline, it increases the octane levels of the fuel which helps the engine to have a higher performance.
The mixtures which have low percentage of ethanol in them are also called gasohol; these do not require any alterations to the engine. As the percentage of ethanol in fuel gets higher, the engine requires more modifications.
Biodiesel
The efficiency of biodiesel is also less than that of gasoline. However, it highly depends upon the quality and blending of the fuel. Biodiesel is labeled with B- as prefix at the gas stations, followed by the percentage of biodiesel in the fuel mix. For example, B20 is 20% biodiesel in diesel fuel.
The lower the percentage of biodiesel added, the lower the need to modify the engine. If we use pure biodiesel, in the long run that would lead to some performance and maintenance problems. These maintenance problems can be taken care of. Biodiesel is more common in European Union than in the US.
Read more on Biodiesels: Biodiesel; Definition, Pros and Cons
How to make your own biofuels?
So far we have given you a highlight of how the production of biofuel happens and how does it work.
Now we are going to make you learn how you can make your own biofuel and replace it with gasoline.
You would never have to visit gas stations again and you can be self-sufficient.
We are going to go into a step by step guide to make biofuel, the startup kits you’ll need and the cost-benefit analysis for you to make a better and safer decision.
10 Steps to make your own biofuel
There are a total of ten steps that would let you have a final product of biofuel that you can use in your car.
1. Finding an oil source
The most basic problem that people face is finding an oil source to start from. Most people go for getting vegetable oil from local restaurants.
But before we get into where we can obtain raw fuel, we have to make sure that the waste oil that we get should;
- Be pre-filtered to around 400 microns
- De-watered
- Have low free fatty acid levels
We would recommend that you obtain waste oil from restaurants that change their oils every week. This will help you to find better-quality oil.
People can also obtain canola, corn, or peanut oils.
Other sources of obtaining waste oil are from animal fat, tallows, or lard. However, we would not recommend that you obtain waste oil from these sources since they have higher ratios of gel point that can cause your engine to clog at higher temperatures.
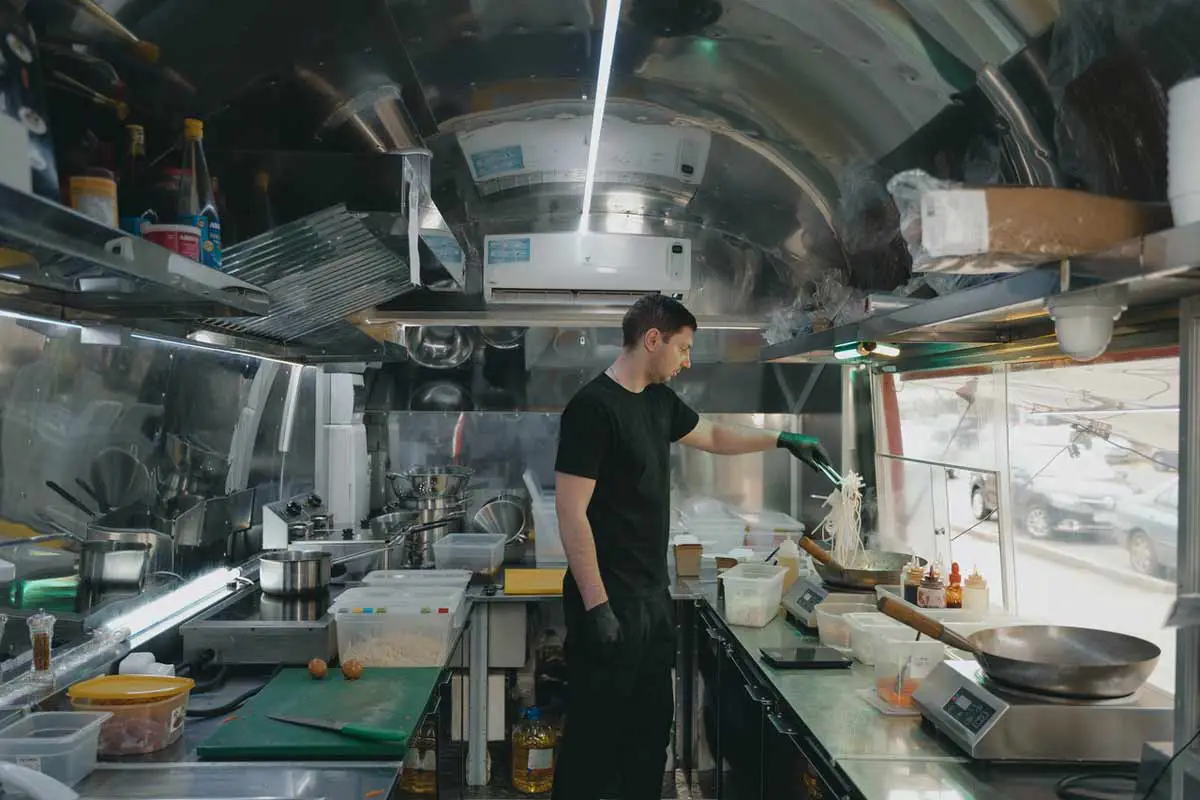
2. Testing the oil
After you get the oil, we need to test its quality to make sure we can use it. It is very important to first test the oil.
There are several types of testing that can be done. The major ones are testing the oil for water and acid.
To test the oil for water, just simply heat it in a pan and look out for bubbles.
To check acidity levels, we need to learn titration.
The method used to check acidity level is called titration. This involves taking a sample of oil and adding it to exactly similar amount of pH-neutral alcohol. Then we would use a pH filter to determine the level of acid, mostly we use Phenolphthalein.
It is very important to check the acidity levels. If the oil contains high acidity levels, the base chemical we add later can then get neutralized by the high level of acid. By knowing the acidity level, we can measure and add the exact base chemical needed to convert it into biofuel.
3. Filtering the oil
Filtering the oil makes it more pure and efficient. We need to make sure that the oil has no food particles and other contaminants in it.
Out of many ways of filtering the oil, we would suggest that you take a 55-gallon drum that has a metal drum filter on it.
The important thing is to know the size of the filters. We would recommend that the smaller the holes, the better. 400 microns filter would work the best.
4. Making a test batch
Before starting off, it would be wise to make a test batch. This will show whether this oil that you just obtained is worth converting into biofuel or not.
It is very easy to make a test batch as everything required for making it are usually available at your nearby grocery stores.
5. Obtaining production equipment
If you have the proper equipment, it is not difficult for you to make biofuel. The list of things that you would require for making all this possible is:
- Oil collection containers: To handle and store the oil obtained. You can recycle an old oil barrel/drum for this. If you can’t find it in the shed, ask a neighbor to lend you one they’re not using. Worst case scenario, visit your nearest scrap yard!
- Oil transfer capability: To transfer oil from the collection area (restaurants) to the area where you’ll be producing oil (Suggestion: Backyard). Usually, your truck can hold the oil barrel.
- Oil filters: To filter out the oil for processing. 400 Microns.
- A biofuel processor: This will help convert your oil into biofuel by mixing chemicals with the oil.
- A biofuel washing vessel: This is used to wash off contaminants from the oil barrel.
- A biofuel storage container: After washing and filtering, you’ll need these to store the filtered oil.
- Transferring pumps: They come in all sorts of shapes and sizes; they are used for transferring oil among different containers.
- Titration kit: To check the acidity level.
6. Obtaining chemicals
As part of the chemical reaction, methanol is used.
Methanol reacts with the waste of vegetable oil in order to make biodiesel.
Other than methanol, you would be required to have Potassium Hydroxide or Sodium Hydroxide. Both of them are available at plumbing stores. We would suggest you to get Potassium Hydroxide, as it makes glycerin runnier and dissolves easily in Methanol.
Any one of these Hydroxides will act as a catalyst to get the chemical reaction between methanol and oil started.
7. Pre-Treating the oil
It is necessary to make sure it is ready to be processed before the oil can be turned into Biodiesel. In Step 2 we discussed measuring water and acid content for the oil.
Now it’s time we explore how to deal with watered oil and/or high acid content.
Dewatering
There are several ways of dewatering oil, the simplest ways of them all is to let the oil settle.
Water and oil really don’t like each other and with enough time the water just sinks to the bottom and can be removed afterwards.
You can also heat up the oil to speed this process. This allows the oil molecules to expand, making it easier for the water molecules to fall out of suspension.
Reducing Acid level
If the oil you get contains high levels of free fatty acids, then you should consider reducing the level of acid in the oil before using it to make Biodiesel. Biodiesel can be made from high free fatty acid feedstock, but it is kind of a hassle.
The explanation is that you end up using so much extra solvent that you will still have plenty of soap to deal with by the time you have Biodiesel.
There are 2 ways to reduce acidity of your oil; Caustic Stripping and Acid Esterification.
Caustic Stripping
This involves dissolving some of the solid base (sodium or potassium hydroxide) into water, and then adding that mixture to the oil. This will cause the oil free fatty acids to bind to the solid base and form soap. The soap is then removed from the oil, the oil is dewatered, and Biodiesel can then be made with it.
Although efficient, this approach will decrease the yield of Biodiesel that you’ll get from it as a portion of the oil is turned into soap.
While caustic stripping is discouraged at some biodiesel factories as a means of reducing free fatty acids, we know it can be done and it’s effective. Some just prefer to use the second method.
Acid Esterification
This process uses sulfuric acid to change the free fatty acids ( FFA’s) in the oil so they can still be transformed into biodiesel. When working with oil that has high free fatty acids, this is the preferred approach. The reason it is chosen is that instead of turning the FFA into soap, it simply modifies the acid chains and makes them transform into biofuel or biodiesel.
8. Processing biodiesel
All of those previous stages were mainly to prepare for this one. This is the main processing of oil into Biodiesel. This is where the magic takes place and where the actual reactions occur, allowing you to create organic oil biodiesel.
It is crucial you practice good safety before we get going. Let’s look at some precautions you’ll need to take.
Precautions
- You’ll be working with some relatively caustic liquids, an alcohol called methanol, a decent amount of heat, and a transition of flammable materials from one container to another. It’s advised to have a fire extinguisher around that is capable of putting out an oil-based burn.
- Biodiesel will ideally be processed in a well-ventilated environment; away from children and pets, with appropriate safety equipment.
- Until producing big quantities of Biodiesel, consult with your local municipality and fire department to insure that all additives, alcohol or other compounds you use are processed and used in compliance with the applicable laws and regulations for your region.
- Using home-made Biodiesel in a diesel engine vehicle may cancel the manufacturer’s warranty. So try it if you have an old truck out of its warranty.
- Biodiesel itself is generally very healthy when properly made. It is less toxic than table salt and it degrades faster than sugar. It has a higher flash point (the point at which it ignites) than normal petro-diesel, and is not considered harmful if spilled.
9. Washing and drying Biodiesel
When Biodiesel is made, we often add more methanol than we need. This is to ensure that the chemical reaction is completed. Once the reaction has happened, much of the methanol is now part of the original Biodiesel (although it’s slightly different now). The excess methanol will end up in the glycerin. There is also a part of the excess methanol that stays in the biodiesel.
Washing Biodiesel
When water is used, the methanol molecules love water more than Biodiesel does.
The water brings the dissolved methanol down into the water sheet, with all the other things sitting on it. Wash it enough and it will wash all that excess methanol right out along with all the other stuff that it was holding on to.
When using a dry-wash system, the same process also occurs essentially. The dry resin or powder absorbs or catches glycerin, soap, & methanol while allowing biodiesel to slip through.
Drying biodiesel
Now that you want to get rid of the water, let’s talk about how to do that.
First off, Biodiesel can be dried with a million different ways. If you make a quick search, you will find them dispersed all over the internet. We’ll just talk about some of the simpler ways to do that for our purposes of making biodiesel.
One of the best ways to do so is to bring your Biodiesel out in the bright sun. Let the magic work with Mother Nature. If the weather is dry enough, the sun’s heat will help evaporate all the water relatively easily.
After drying, and removing glycerin, your biodiesel is ready for use.
10. Dealing with Glycerin
The glycerin waste can be given to waste management plants.
The plant possesses a special processing system called an Anaerobic Digester (Also known as a Methane Digester).
Basically, all of the raw sewage is mixed up into a large mixing machine and then transferred to a large tank where bacteria feed on and break down the raw sewage.
The bacteria then produce methane gas as a by-product. The methane is caught and incinerated in the methane power plants.
Crude glycerin serves to the bacteria as food and triggers further methane production. As a result, the waste management plant was able to take all of our glycerin and we now have an eco-friendly way to get rid of all of it.